Centrifuge
1. General overview
1.1. Introduction
The centrifuge makes it possible to refine the cleaning of the material by removing the last impurities (tape, labels, dust, sand, etc.) and the humidity present after the washing step.
Today centrifugation techniques are very common in industry. There are several types of centrifuges but they often have complex geometries and therefore are difficult to replicate.
As with the shredder, the objective was to design, in the Plastic Odyssey workshop, a machine that can be built with simple materials found all over the world, with minimum technical skill and without complex tools.
The role of the centrifuge
The so-called vertical centrifuge separates the last impurities and water from the shredded plastic or more precisely expels them through a grid. All that remains is the dried plastic chips, ready to be stored.
The centrifugal effect is actuated by a rotating cylinder equipped with helical fins. This drives the plastics in a circular motion which projects them against a grid arranged all around the cylinder. The separation takes place during the projection where water and the last impurities are ejected outside the cylinder through the screen, while the larger chips remain inside.
1.2. The centrifuge on board the Plastic Odyssey
The Plastic Odyssey centrifuge has been developed for more than two years in Marseille.
It is the result of many encounters. In particular with recycling centers encountered locally, close to waste deposits in Cairo, Burkina Faso and Thailand.
It is the result of numerous meetings with experts. That means; a robust, efficient machine capable of handling all types of waste, but above all productive.
Why low-tech? In regards to its manufacturing process: a simple design, the use of universal tools and standard materials.
2. Technical guide
2.1 Technical datasheet
General characteristics
Motorisation
Process
Economic and environmental
Manufacturing
2.2. Connections and Sockets
Network Connections
Sockets
3. User guide
3.1. Preparation
Mandatory protection:
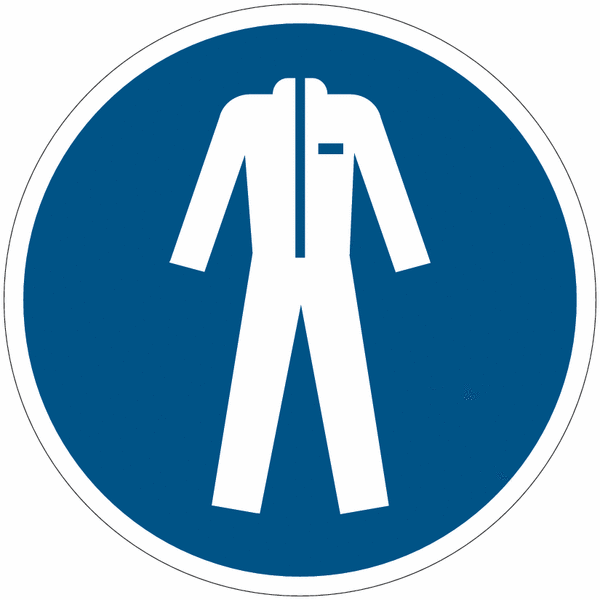
Protective gloves
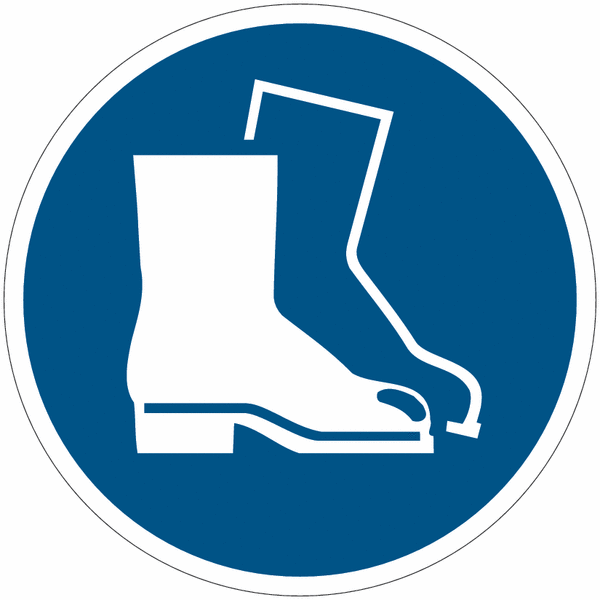
Safety shoes
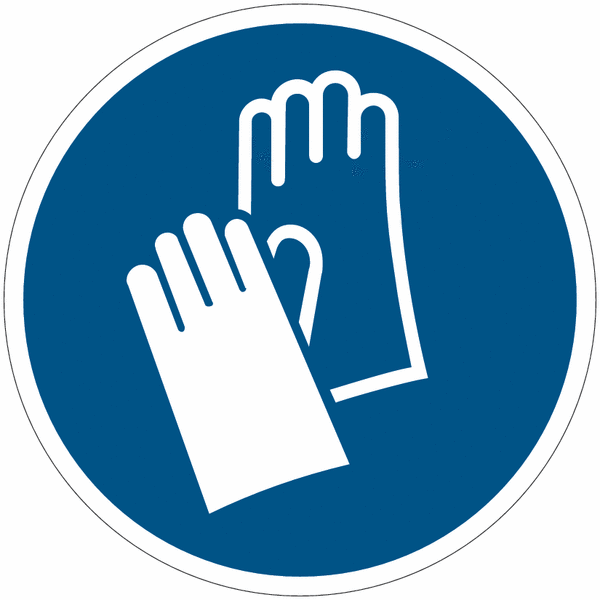
Protective gloves
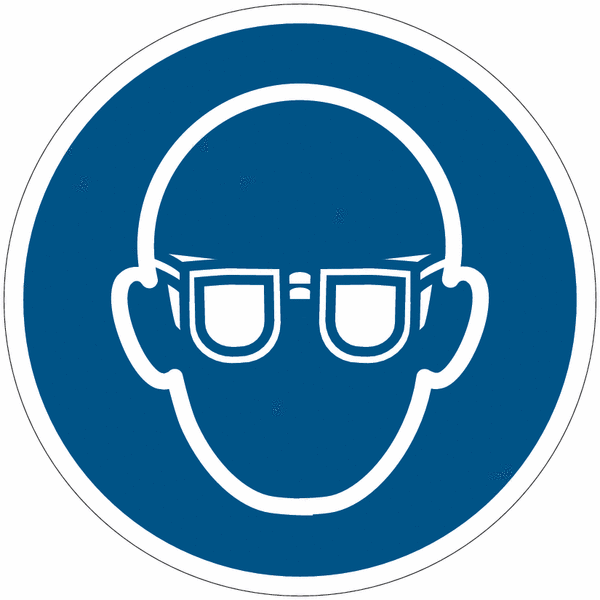
Safety glasses
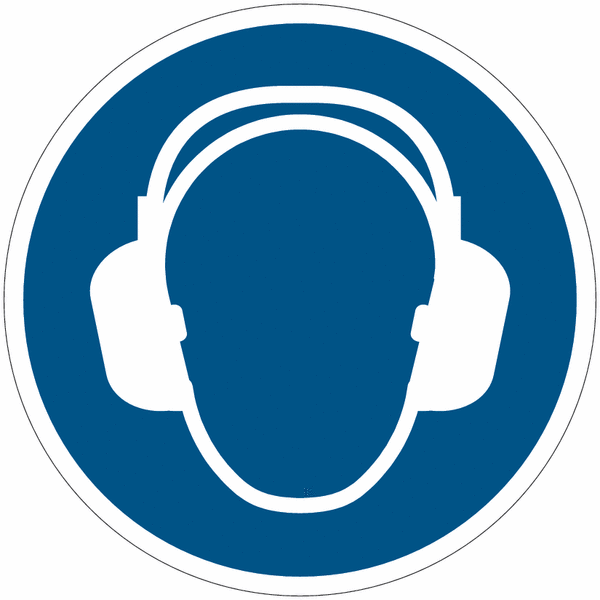
Noise cancelling ear muffs
Necessary Equipment:
- A collection bag for the granualte
- A water pipe
- An air compressor
- A filtration system for waste water
Good practices:
- Place a collection bag under the cyclone before starting the centrifuge
- Introduce the plastic granulate into the hopper gradually
- Respect the type of material to be introduced into the machine
- Regularly check the level of the pollutant retention tray
- Turn off the centrifuge to empty the water and pollutant retention tank
- Treat the polluted water
- Do not put your hands in the feed hopper
- Ensure you have read the information specified in the information sheets: Jobsite Information Sheet, Safety Sheet
Verification
Before any use, visually check the mechanical condition. Periodically check the condition of the equipment (see maintenance sheet).
3.2. Usage
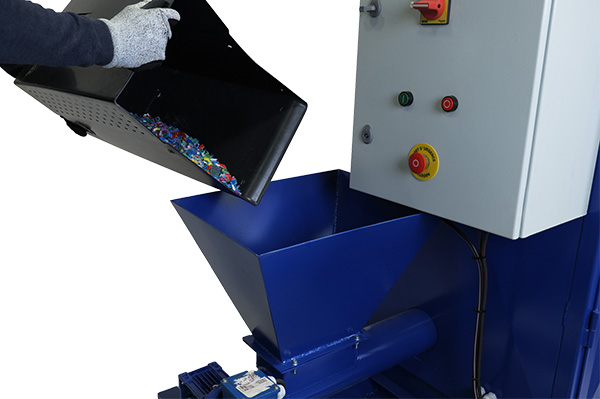
- Add the plastic granaualte into the hopper
The presence of an operator is needed at all times to ensure the flow of material.

- Change the granualte collection bag when it is sufficiently full
Stop introducing plastic into the hopper beforehand, then stop the engine before removing the bag.
- Close the collection bag
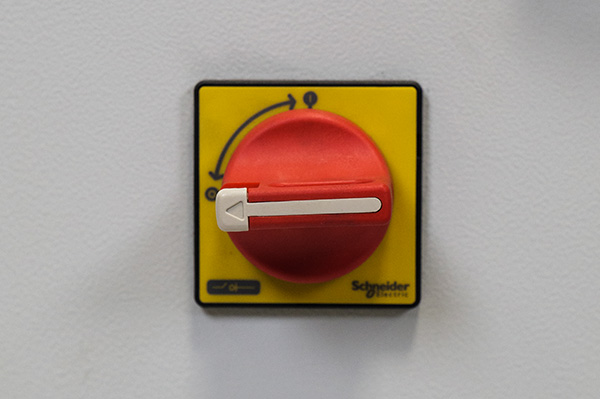
Shutdown procedure:
- Let the machine absorb all the waste still present in the hopper
- Cut the power to the motor using the OFF button
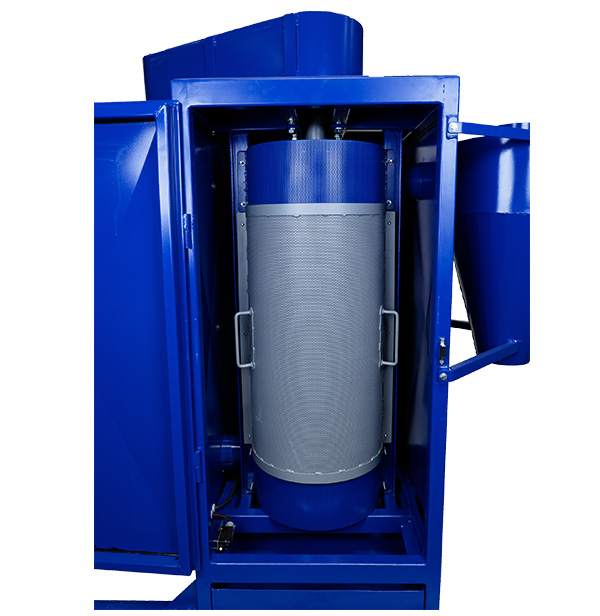
- Blow compressed air inside the hopper
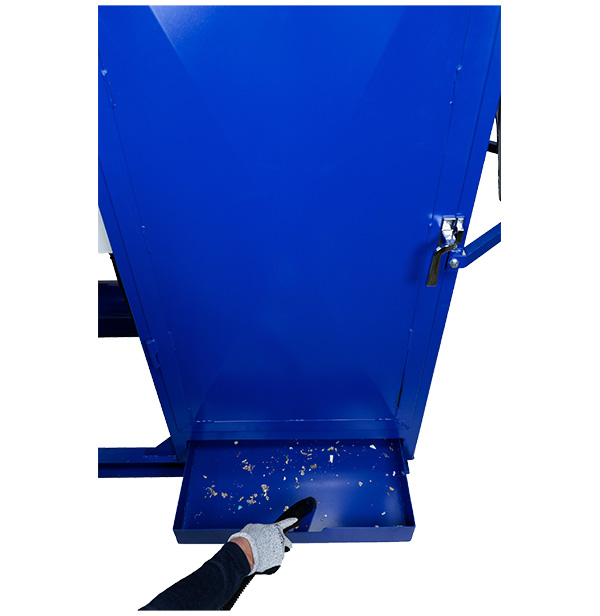
- Empty and clean the collection bin
- Close recovery bag
4. Safety
4.1. Training
The operators who interact with the centrifuge must be aware of and respect the information relating to the use of the machine, the risks of using the machine, and the appropriate safety practices.
4.2. Risks
- Crushing of fingers by the feed screw
- Winding / entanglement of clothes or objects due to the rotating system
- Projection of plastic chips
- Cuts due to handling rough chips
4.3. Operator behavior
- Do not put your hands in the hopper
- Observe the type of material admissible by the centrifuge
4.4. Personal protective equipment
- Safety shoes are compulsory throughout the workshop and around all the machines.
- The operator has to handle plastic chips which can be rough, protective gloves are therefore mandatory to handle the chips safely.
- Plastic chips can occasionally be violently thrown, therefore protective goggles must be worn.
- The centrifugation of plastic waste generates a lot of noise. Ear muffs or ear plugs are necessary to protect the operator from the surrounding noises.
- The operator must wear suitable work clothes.
4.5. Safety features
Safety features guarantee the safety of operators on the centrifuge. Make sure they are correctly installed before use:
- The two enclosure doors are closed and locked.
- The belt guard is correctly positioned and secured.
4.6. Work zone
A work zone around the machine is defined by a marking on the ground.
Access near the machine, whilst it is in operation, is permitted only to trained and equipped operators.
4.7. Jobsite information Sheet
The centrifuge is equipped with a Jobsite Information Sheet which includes all the information necessary for the use of the machine in good safety conditions. It must be positioned in view of all operators using the centrifuge.
4.8. Verification/Maintenance
Preventive and corrective maintenance activities must only be carried out by a person trained for this purpose. Each intervention must be recorded in order to keep a history of the maintenance actions carried out.
5. Cleaning and Maintenance
5.1. Maintenance schedule
Day to day
Weekly
Monthly
Yearly
5.2. Cleaning schedule
Day to day
Weekly
Monthly
Yearly
5.3. Intervention protocol
Before performing any maintenance, adjustment or repair operation requiring partial or complete disassembly of centrifuge components, it is necessary to follow these protocols before the operation.
Electrical
- Set the power button to Off
- Activate the emergency stop button, and if accessible, switch off the main power
- Mechanically block the power button with a padlock
- Check the absence of voltage on each of the active conductors (including the neutral) using a specially designed VAT device
Mechanical
- Wait for the rotors and fans to come to a complete stop
- Uncouple the belts
- Mechanically block the rotor
- Visually check for dissipation of motor force and immobilization of moving parts