Barrel
The barrel is the support of moulds allowing to realize profiles of various sizes and sections.
1. General overview
1.1. Introduction
The barrel is a complementary tool to the extruder. It facilitates the shaping of the molten plastic at the end of the extrusion. It is a low-tech solution for molding large profiles of various lengths and sections, at a rate that meets industry standards.
Extrusion lines can reach tens of meters in length, requiring suitable infrastructure. To reduce this infrastructural stress, the barrel allows a continuous profile manufacturing process within limited space. It also has the advantage of being able to accommodate profiles of various sizes and sections by simply changing molds.
The role of the barrel
The barrel is a support which allows several molds to be fixed. When the molten plastic has filled a first mold, a simple rotation presents a new empty mold at the exit of the extruder so as not to interrupt the process. Once filled, the plastic contained in the mold is cooled in air and / or in water before being removed from the mold and then creating large profiles.
1.2. Barrel on board the Plastic Odyssey
The barrel was designed in the Plastic Odyssey workshop in Marseille. It is a low-tech, efficient, easy-to-use system that can easily be adapted to the dimensions of any recycling center.
2. Technical guide
2.1 Technical datasheet
General characteristics
Process
Economic and environmental
Manufacturing
3. User guide
3.1. Preparation
Mandatory protection:
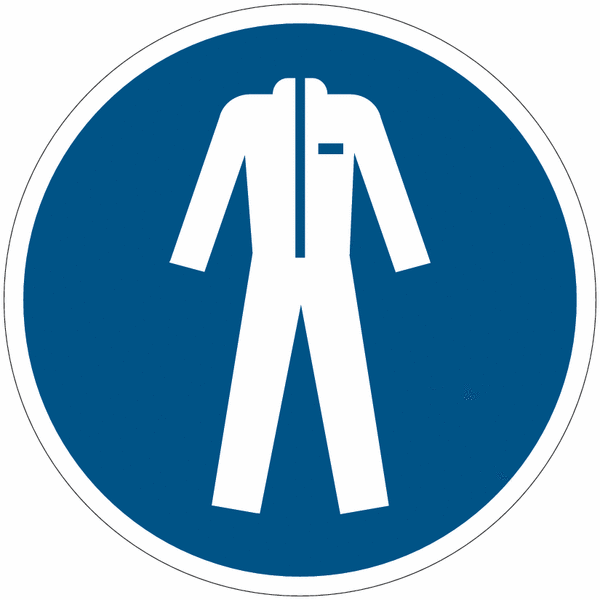
Coveralls
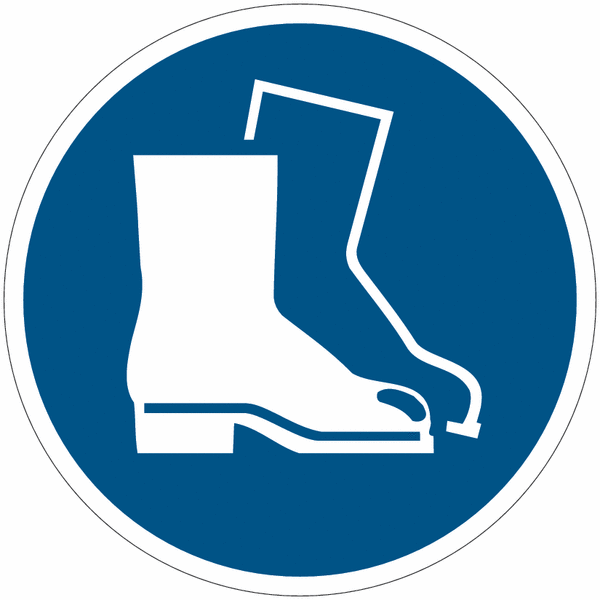
Safety shoes
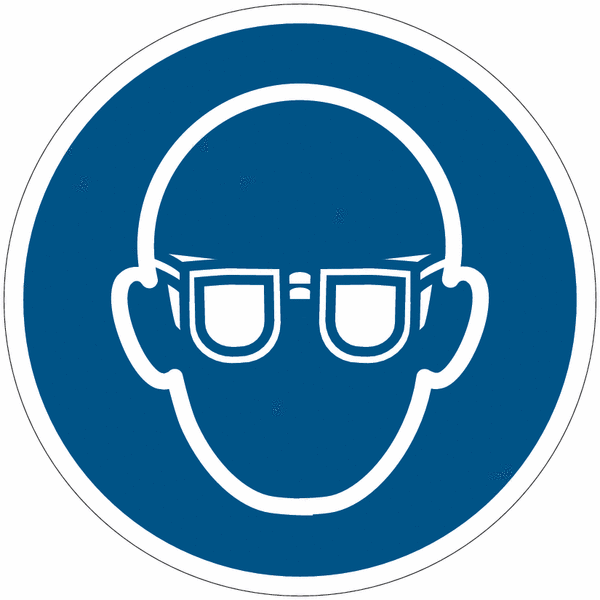
Safety glasses
Necessary Equipment:
- A pair of heat-resistant gloves
- A set of flat wrenches
- An allen key set
- A water pipe
Good practices:
- Fix the profiles on the barrel
Verification
Before any use, visually check the mechanical condition. Periodically check the condition of the equipment (see maintenance sheet).
3.2. Usage
- Fill the cooling tray
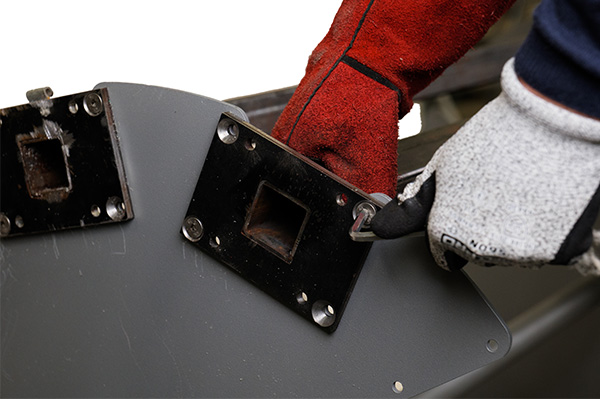
- Fix the profiles on the barrel
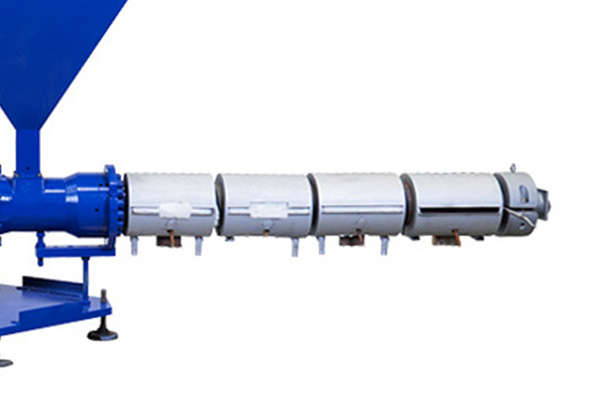
- Position and clamp the profile to be filled in front of the extrusion nozzle
- Watch until the profile is full
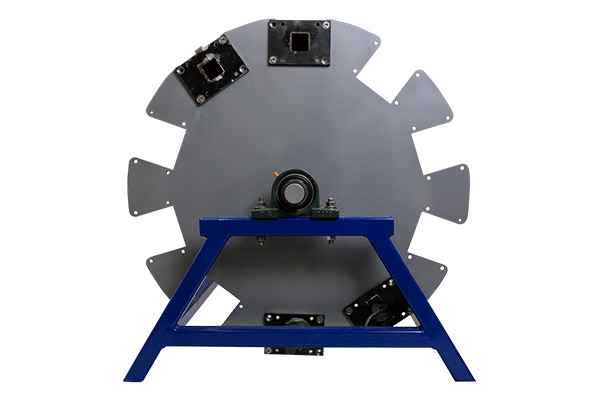
- Once the profile is filled, uncouple it
- Rotate the barrel to the next profile
- Repeat the previous steps for the other profiles
- Demold the profiles when they have cooled to a sufficient temperature
4. Safety
4.1. Training
The operators who interact with the barrel must be aware of and respect the information relating to the use of the machine, the risks of using the machine, and the appropriate safety practices.
4.2. Risks
- Winding / entrainment of clothes or objects due to the rotating system
- Burns due to the handling of elements in contact with the extruded plastic
4.3. Operator behavior
- Handle the barrel and the profiles with heat resistant gloves
- Use the brake system to control the rotation of the barrel
4.4. Personal protective equipment
- Safety shoes are compulsory throughout the workshop and around all the machines.
- The operator has to handle parts that contact with the extruded plastic, so heat resistant gloves are mandatory.
- The operator must wear suitable work clothes.
4.5. Safety features
Safety features guarantee the safety of operators on the barrel. Make sure they are correctly installed before use:
- A brake system is installed on the barrel to control the rotation of the profiles.
4.6. Work zone
A work zone around the machine is defined by a marking on the ground.
Access near the machine, whilst it is in operation, is permitted only to trained and equiped operators.
4.8. Verification/Maintenance
Preventive and corrective maintenance activities must only be carried out by a person trained for this purpose. Each intervention must be recorded in order to keep a history of the maintenance actions carried out.