Sheet Oven
Transforming plastic waste into a sustainable material to give life to new 100% recycled products.
1. General overview
1.1. Introduction
The Sheet oven is a simple solution for transforming plastic waste into sheets with interesting mechanical properties and in a wide range of colors, patterns and thickness.
The advantages of recycled sheets are many. They work like wood, they can be cut, sanded and drilled. Therefore it is a material offering a variety of solutions for designing everyday products or building materials made from 100% recycled plastics.
The role of the sheet oven
The plastic previously crushed, cleaned and then dried is placed in a mold, allowing the material to be given a desired shape Under the effect of heat, the shredded plastic will then bind together to create a rigid plate.
In order to obtain smooth and compact sheets, the molten material in the mold must then be compressed. This can be done using a hydraulic press.
1.2. The sheet oven on board the Plastic Odyssey
The oven was developed in the Plastic Odyssey workshop in Marseille.
The objective was to build a low-tech heating system allowing the production of sheets with the following dimensions: 1 x 0.60 m Depending on the size of the sheet desired, the Sheet oven can be commercial or custom made.
In order to optimize space in the recycling workshop, its design integrates the ability to be adapted into a mobile workbench to provide a work surface and storage space.
The essential elements of the oven are the heating elements and insulation. The heating system is important for optimizing cycle times and the insulation helps reduce heat and energy loss. The oven has a door and sheep wool insulation, an organic and effective solution.
2. Technical guide
2.1 Technical datasheet
General characteristics
Heating System
Process
Economic and environmental
Manufacturing
2.2. Connections and Sockets
Network Connections
Sockets
3. User guide
3.1. Preparation
Mandatory protection:
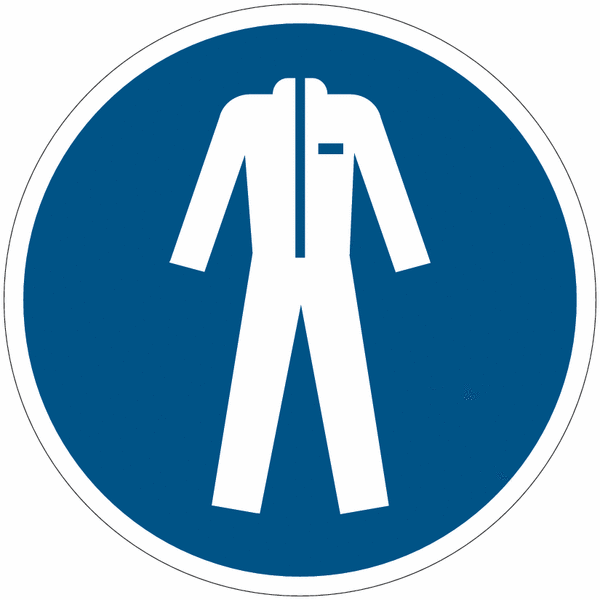
Protective gloves
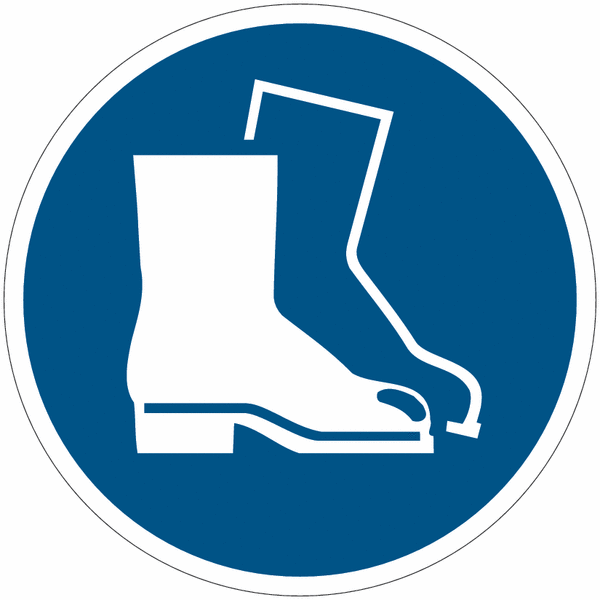
Safety shoes
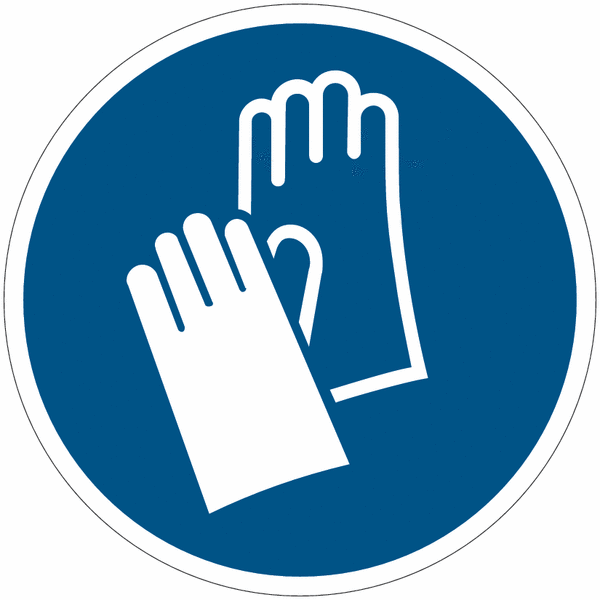
Protective gloves
Necessary Equipment:
- Heat resistant gloves
- A sheet mould
- A release agent
- Bucket
Good practices:
- Apply both brakes to immobilize the Sheet oven during use
- Close the oven door when it is heating
- Respect the heating temperatures
- Use a mold to process the plastic
- Do not put your hands inside the sheet oven
- Ensure you have read the information specified in the information sheets: Jobsite Information Sheet, Safety Sheet
Verification
Before any use, visually check the mechanical condition. Periodically check the condition of the equipment (see maintenance sheet).
3.2. Usage
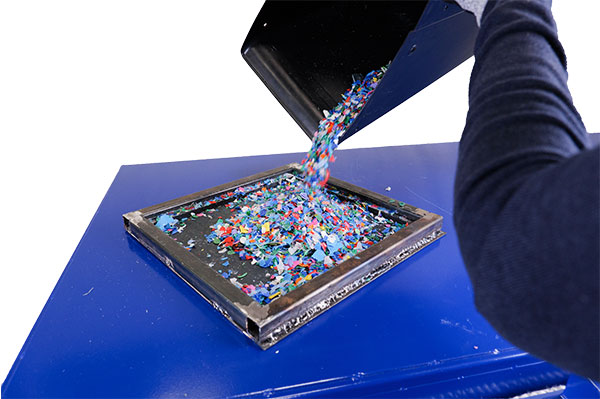
Prepare the mold:
- Apply the release agent
- Pour in the plastic shavings
- Close the mold
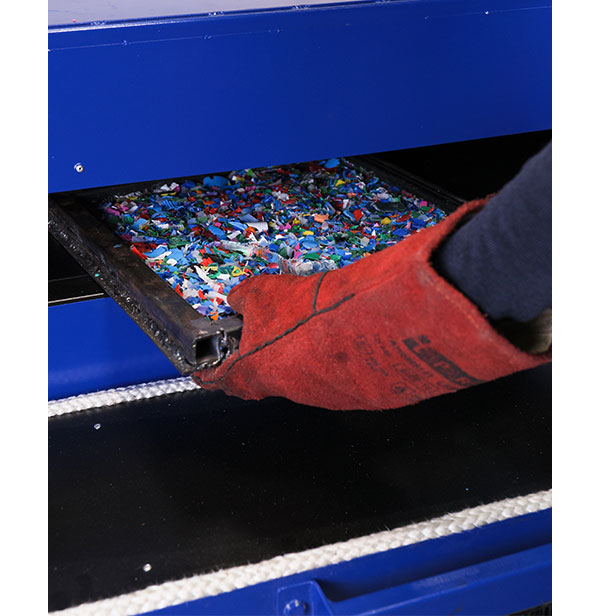
The oven is at the right temperature:
- Open the oven door
- Put the mold in the oven
- Position the mold in the center of the heating zone
- Close the oven door
- Monitor cycle time
- Check the homogeneity of the molten plastic
- If the cycle is finished, turn off the resistors
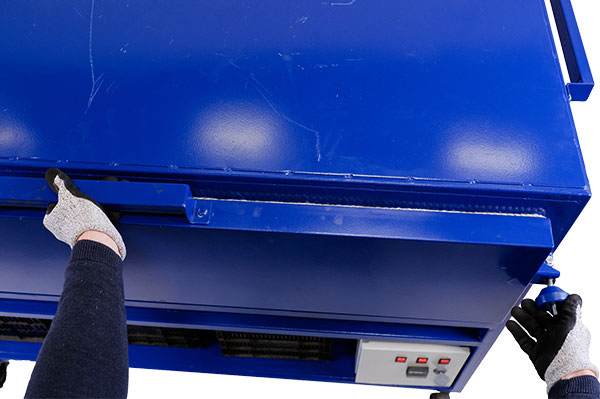
- Take out the mold
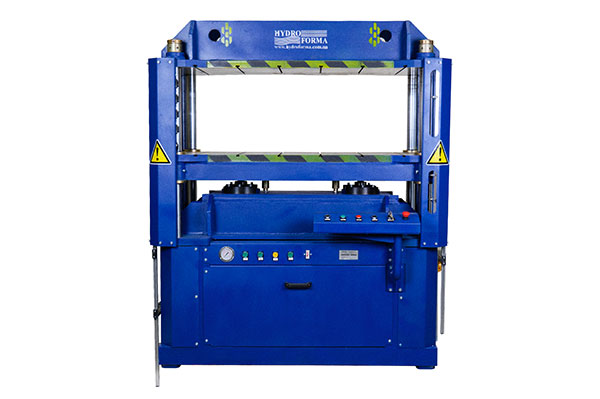
To obtain a plate, you must then:
- Press the mold using a hydraulic press (see: hydraulic press)
- Unmold the plastic plate
- Clean the mold
4. Safety
4.1. Training
The operators who interact with the sheet oven must be aware of and respect the information relating to the use of the machine, the risks of using the machine, and the appropriate safety practices.
4.2. Risks
- Burns due to handling high temperature parts
- Cuts due to handling rough chips
- Crushing of fingers associated with handling molds
4.3. Operator behavior
- Handle the molds with heat resistant gloves.
- Do not touch the heating elements or the interior walls of the oven.
- At the end of heating, take care when opening the door. Allow the hot air to gradually escape from the oven before you enter it.
- Refrain from placing heavy objects on the door to avoid damaging it.
4.4. Personal protective equipment
- Safety shoes are compulsory throughout the workshop and around all the machines.
- The operator has to handle plastic chips which can be rough, protective gloves are therefore mandatory to handle the chips safely.
- The operator has to handle parts at high temperatures, so heat resistant gloves are mandatory.
- The operator must wear suitable work clothes.
4.5. Work zone
A work zone around the machine is defined by a marking on the ground.
Access near the machine, whilst it is in operation, is permitted only to trained and equipped operators.
4.6. Jobsite information Sheet
The sheet oven is equipped with a Jobsite Information Sheet which includes all the information necessary for the use of the machine in good safety conditions. It must be positioned in view of all operators using the oven
4.7. Verification/Maintenance
Preventive and corrective maintenance activities must only be carried out by a person trained for this purpose. Each intervention must be recorded in order to keep a history of the maintenance actions carried out.
5. Cleaning and Maintenance
5.1. Maintenance schedule
Day to day
Weekly
Monthly
Yearly
5.2. Cleaning schedule
Day to day
Monthly
5.3. Intervention protocol
Before carrying out any maintenance, adjustment or repair operation requiring partial or complete disassembly of elements of the plate oven, it is necessary to follow these protocols before the intervention.
Electrical
- Set the power button to Off
- Activate the emergency stop button, and if accessible, switch off the main power
- Mechanically block the power button with a padlock
- Check the absence of voltage on each of the active conductors (including the neutral) using a specially designed VAT device.